Spider weight mold is a crucial concept in the realm of manufacturing and design, particularly for those involved in the production of lightweight components. As industries advance, the demand for innovative and efficient molding techniques has grown exponentially. This article delves into the intricacies of spider weight molds, exploring their applications, advantages, and best practices for implementation.
In this comprehensive guide, we will cover various aspects of spider weight molds, including their design principles, materials used, and the latest trends in the industry. Whether you are a seasoned professional or a newcomer to the field, this article aims to provide valuable insights that will enhance your understanding and application of spider weight molds.
By the end of this article, you will have a thorough grasp of spider weight molds and their significance in modern manufacturing. We encourage you to explore the information presented and consider how these techniques can be applied to your projects.
Table of Contents
- What is Spider Weight Mold?
- The Biology of Spider Weight Mold
- Applications of Spider Weight Mold
- Advantages of Using Spider Weight Mold
- Design Principles for Spider Weight Molds
- Materials Used in Spider Weight Molds
- Current Trends in Spider Weight Molding
- Conclusion
What is Spider Weight Mold?
Spider weight mold refers to a specialized molding technique used in manufacturing lightweight components. This method employs a unique design that resembles a spider's web, allowing for the efficient distribution of weight across the mold. The primary goal of using a spider weight mold is to create products that are not only lightweight but also structurally sound.
In engineering and manufacturing, understanding the mechanics behind spider weight molds can significantly impact the production process. By utilizing this technique, manufacturers can reduce material costs while maintaining high-quality standards, ultimately leading to improved product performance.
The Importance of Spider Weight Mold in Manufacturing
The significance of spider weight mold lies in its ability to enhance efficiency and reduce waste. As industries strive for sustainability, the need for lightweight components has become paramount. Spider weight molds allow manufacturers to create products that meet these demands without compromising on strength or durability.
- Efficiency in production
- Reduction in material waste
- Improved product performance
The Biology of Spider Weight Mold
Understanding the biological principles that underpin spider weight mold can provide deeper insights into its applications. The structure of a spider's web is an excellent analogy for the design of these molds. Just as a spider’s web is engineered to support weight while remaining lightweight, spider weight molds are designed to achieve similar results in manufacturing.
Research has shown that the intricacies of spider silk, including its tensile strength and flexibility, can inspire new materials and designs in the manufacturing industry. By studying these natural structures, engineers can create more efficient and effective molding techniques.
Applications of Spider Weight Mold
Spider weight molds find applications across various industries, including:
- Aerospace
- Automotive
- Consumer electronics
- Medical devices
In the aerospace industry, for instance, the use of lightweight materials is critical for improving fuel efficiency and performance. Spider weight molds facilitate the creation of components that meet these requirements while ensuring safety and reliability.
Advantages of Using Spider Weight Mold
The advantages of utilizing spider weight molds are manifold:
- Enhanced structural integrity
- Weight reduction
- Increased design flexibility
- Cost-effectiveness
By implementing spider weight molds, manufacturers can innovate while optimizing their production processes, leading to a competitive edge in the market.
Design Principles for Spider Weight Molds
When designing spider weight molds, several key principles should be considered:
- Load distribution: Ensure even weight distribution across the mold to enhance performance.
- Material selection: Choose materials that complement the design and desired properties.
- Manufacturability: Design molds that are easy to produce and maintain.
Adhering to these principles will yield optimal results and improve the overall efficiency of the molding process.
Materials Used in Spider Weight Molds
The selection of materials is critical in the creation of spider weight molds. Common materials include:
- Aluminum
- Steel
- Composite materials
Each material offers unique properties that can enhance the performance of the mold, such as weight, strength, and durability. Understanding these materials will enable manufacturers to make informed decisions that align with their production goals.
Current Trends in Spider Weight Molding
As industries evolve, new trends in spider weight molding continue to emerge:
- Increased use of advanced composites
- Integration of smart technologies
- Sustainability initiatives
Staying abreast of these trends will empower manufacturers to adopt innovative practices that enhance their production capabilities and meet market demands.
Conclusion
In conclusion, spider weight mold is a vital technique in modern manufacturing that offers numerous advantages, including weight reduction and enhanced structural integrity. By understanding its applications, design principles, and materials, manufacturers can leverage this technique to improve their production processes.
We encourage readers to explore further and consider how spider weight molds can be integrated into their projects. Leave a comment below or share this article with colleagues to foster discussions on the topic!
Call to Action
For more informative articles on manufacturing techniques, subscribe to our newsletter and stay updated with the latest trends and insights in the industry!

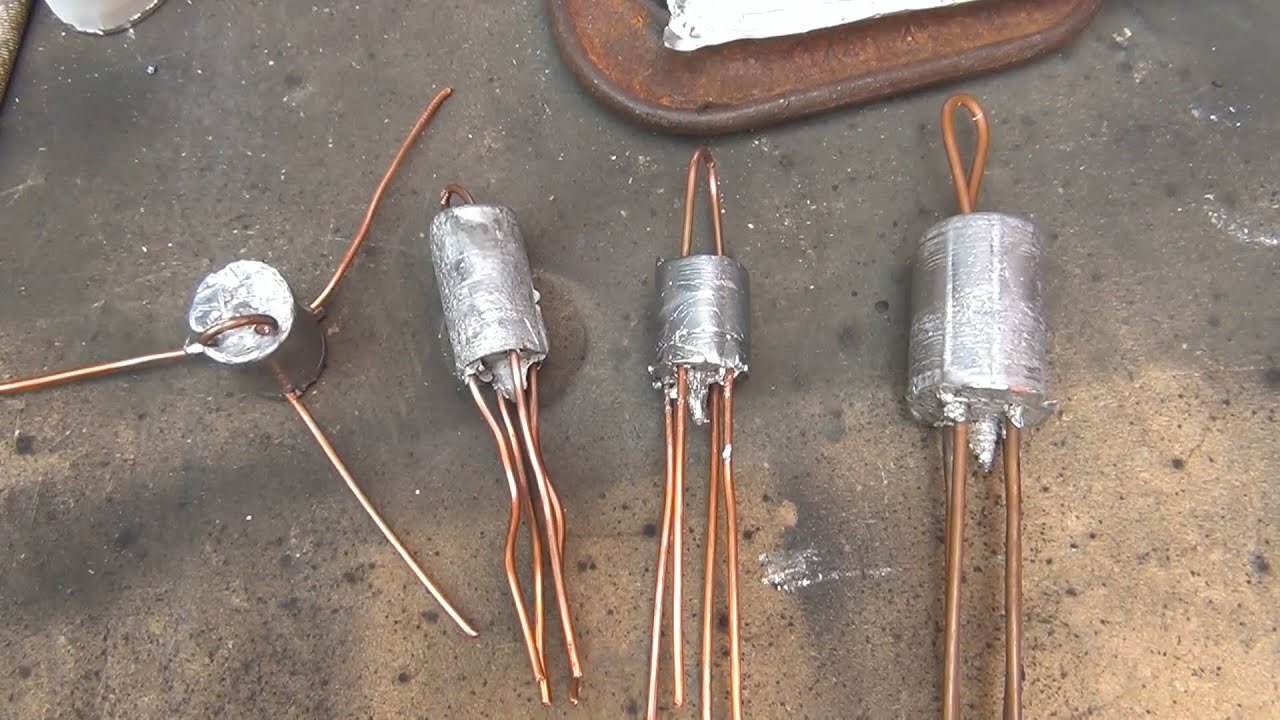